Owners and contractors are encouraged, incentivized, and rightfully pushing to build a more sustainable future by utilizing materials that can withstand the test of time while limiting global environmental impacts. All material producers of the construction world are digging into this topic headfirst: wood, steel, concrete, and more. Concrete is often at the forefront of everyone's mind since it is the most common building material and seemingly one of the most environmentally harmful. Traditional concrete, however, is fairly sustainable over the entire lifespan of a project; but with current advancements, it is even more sustainable on the front end and the lifespan!
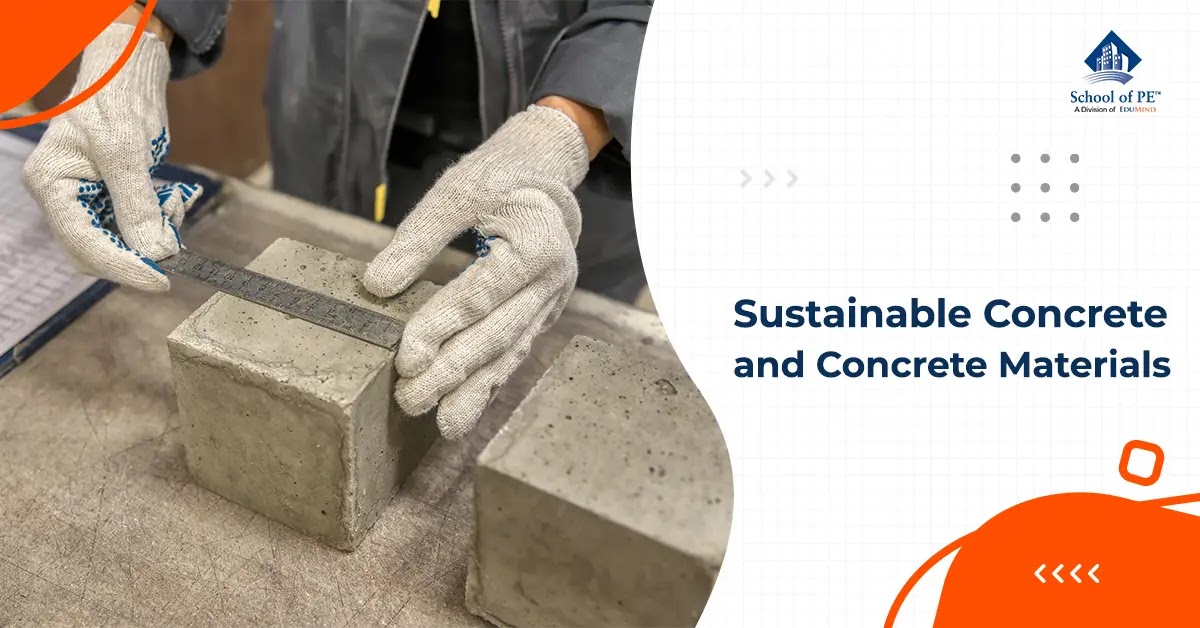
1. Primary Materials
The first topic to investigate is: what are the primary materials concrete is made from? Once we establish this, we can track each item and determine the environmental impact of the material itself.
1. Water
a. We all know what water is but may not know how important it is in a concrete batch. Water interacts with cement, hydrating the particles. This helps create a bond between the other materials. About 18% of a concrete mix is water.
2. Cement
a. Cement is the glue that bonds the elements of a concrete mix. It is typically produced by chemically combining various minerals with limestone, clay, slag, iron ore, and other similar materials. All these ingredients are heated, solidified, and crushed into the cement powder many of us are familiar with. Cement accounts for approximately 10% of a mix.
3. Fine Aggregates
a. Various sizes and colors of sand are what most typically make up the fine aggregate portion of the mix. The quantity of sand varies greatly between mixes, but 25% is the average value.
4. Coarse Aggregates
a. Coarse aggregates are most commonly different types, shapes, sizes, and colors of stone. Rounded stones can be used as well as sharp/jagged stones, depending on the desired properties of a concrete mix design. Similar to fine aggregates, coarse percentages vary greatly but can be considered near 40%.
5. Air
a. Finally, air is the last product that completes a standard concrete mix. Air percentages vary as well, depending on the region of the country you are in. 6% is a common value.
Many of these materials are common and may not require scrutinous environmental impact studies to determine how sustainable they are. However, cement is a manufactured product that does contribute greatly to the environmental impact of concrete and will be the material of focus.
2. Carbon Analyzation Methods
Before investigating cement and its environmental impacts, it is important to understand the methods by which embodied carbon is analyzed and what embodied carbon means. Embodied carbon "is the sum of greenhouse gas emissions released during the lifespan of a product or system" (Structural Engineering Institute). This analysis can be completed either by a method called cradle-to-gate or cradle-to-grave.
- Cradle-to-gate
a. This includes everything leading up to and including the production of a product but nothing thereafter. For concrete, it would be the gathering/production of the raw materials (listed above), the transportation of the materials to the location of the concrete mixing plant, and the mixing/production process.
- Cradle-to-grave
a. This encompasses everything from cradle-to-gate including additional transportation to a job site, the construction of the structure, the use and maintenance of the structure, repairs and refurbishment activities on the structure, and the demolition and disposal of the structure at the end of its life cycle.
Concrete's embodied carbon is typically much higher when looking at a cradle-to-gate analysis, but when looking over the entire lifespan (cradle-to-grave) it performs very well: even while using traditional methods. In brief, concrete lasts a long time and is an excellent insulator!
3. Industry Advancements and Replacement Materials
Traditional cement is outlined above, but advancements in the industry have led to different methods to produce cement that has less embodied carbon than in the past. One of these methods is PLC: Portland Limestone Cement. PLC uses up to 15% limestone, whereas regular Portland Cement uses only 5%. Basically, cement is made the traditional way, but then limestone is added at the end to take up a larger percentage, thus decreasing the embodied carbon in the process since less volume of cement is needed to be produced. When you're looking at the large scale of concrete construction, a change like this is significant!
Another common practice is to replace cement with other cementitious materials. The American Concrete Institute (ACI) has specifications on various cementitious materials, with some of the more common being fly ash, natural pozzolan, slag cement, and silica fume. These materials can often decrease the embodied carbon of concrete because many of them are the waste products of another production line. For example, fly ash is a byproduct in power plants as a result of burning coal, and silica fume is a byproduct from the production of various alloys. By using these cement replacements, the need to produce more cement is lowered and increased sustainability is achieved!
Both of these methods of traditional cement replacement have been tested and used for many years. Limestone cement has been used in Europe and Canada for over 50 years. It wasn't until shortly after 2010 that the United States started seeing code regulations and acceptance of limestone cement. Strength and durability are matched or heightened, permeability is similar, all the resistance properties can be achieved, and nearly all the states have accepted its use or are planning to accept them soon. Similarly, other cementitious materials have been used for hundreds of years: the ancient Romans used volcanic ash as a cement to build many of their concrete structures, and they are still standing today!
4. Concrete as Insulation
Utilizing concrete for a climate-controlled building significantly reduces the embodied carbon over the life of a structure. We touched on this earlier, but concrete has excellent thermal capabilities. The operation of buildings contributes a massive portion of embodied carbon in a cradle-to-grave analysis of a structure. If concrete is used, this can be reduced significantly. Furthermore, if concrete "sandwich" panels are used the savings are even greater! Sandwich panels can be thought of as the "bread" being concrete and the "meat and cheese" being insulation: the thickness of the interior and exterior concrete as well as the insulation can vary to achieve greater R-Values. R-value is the thermal resistance of a material, the higher the value the greater amount of heat flow reduction. Some examples of materials are found below (Ecoline Windows) (D'Aloisio, J.) (Precast/Prestressed Concrete Institute):
- Insulation: 2-6 per inch
- Wood: ~1 per inch
- Concrete: 0.05-0.10 per inch
- Standard double-pane window: ~3
- Steel: 0.0031 per inch
As you can see, if you combine several inches (3 or more) of concrete on either side of the insulation you can achieve a high R-Value very quickly. For example, an insulated wall panel with 2" of extruded polystyrene insulation between 3" of concrete on either side has an R-Value of nearly 11.5! With a high R-Value in the concrete wall (without any additional work being done like lining or spraying it with insulation), less wasted heating or cooling with escape the building.
5. Concrete as a Carbon Sink
Did you know that concrete can actually soak up carbon in the atmosphere?! Carbonation is the process where carbon dioxide "enters tiny pores in the cement and encounters a variety of chemicals and water and becomes trapped. (Cornwall, W.)" Research on just how much carbon dioxide has been soaked up found that "between 1930 and 2013, cement soaked up 16 gigatons of carbon dioxide, 43% of the total carbon emitted when limestone was converted in cement kilns (Cornwall, W.)." Further research is being done to increase the carbon-soaking capabilities of concrete, but even without furthering this technology, our concrete buildings are already working towards a sustainable future!
Conclusion
Sustainable materials are critical to the continuation of our lives as we know it here on Earth. The materials that make up a concrete mix, their transportation, production, construction, and life span all affect the determination of the sustainability of a structure. Combining that with the properties concrete provides and the advancements in the industry prove that concrete is here to stay. Although concrete, through surface analysis, may look like an enemy to sustainability, a deeper look shows that it can truly propel and sustain us into the future.
References
Structural Engineering Institute. What is embodied carbon? SE2050. (n.d.). Retrieved March 13, 2023, from https://se2050.org/resources-overview/embodied-carbon/what-is-embodied-carbon/.
Ecoline Windows. Triple pane windows vs. double pane: What's better? Ecoline Windows. (2022, February 4). Retrieved March 13, 2023, from https://www.ecolinewindows.ca/triple-pane-windows-vs-double-pane-window-features-and-comparison/#:~:text=Double%2Dpane%20windows%20have%20an,paned%20windows%20reduces%20heating%20costs
D'Aloisio, J. (2009, March 8). Envelop the structural steel! Greener Structures. Retrieved March 13, 2023, from https://jdaloisio.wordpress.com/2009/03/08/envelop-the-structural-steel/
Precast/Prestressed Concrete Institute. (2017). Pci Design Handbook: Precast and prestressed concrete.
Cornwall, W. (n.d.). Cement soaks up greenhouse gases | science | AAAS. Science. Retrieved March 13, 2023, from https://www.science.org/content/article/cement-soaks-greenhouse-gases
No comments :
Post a Comment