In general, engines convert heat energy into mechanical energy by exploiting gas onto the piston and crankshaft assembly. The amount of energy depends on the rotational speed of crank shafts as per specifications. An internal combustion engine (ICE) is more efficient than a steam engine because an ICE is simple to start and disengage. An ICE is widely used in the field of transportation.
Important components of internal combustion engines include:
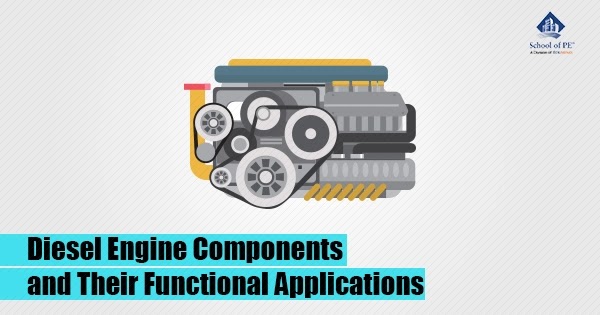
1. Fuel System
In an engine, fuel reaches the cylinder bore through the following path:
Fuel tank -> Water separator -> Feed pump -> Filter -> Injection pump -> Injector nozzle -> Cylinder
- The fuel tank is for storing fuel. Generally, it is made of sheet metal. Most fuel tanks have a fuel gauge to check the fuel level and a drain plug to drain fuel.
- The water separator is used for separating dirt and water from the fuel.
- The feed pump is used to feed fuel to the filter and injection pump.
- The fuel system must pressurize the fuel to open the nozzle. The pressure required to inject fuel into the combustion chamber to offset the pressure of compression is typically 350 to 450 psi. This work is mainly done by the injection pump.
- The injector nozzle injects fuel into the combustion chamber. The injector nozzle atomizes fuel, which is the breaking up of fuel into small particles. The fuel must be atomized when it enters the combustion chamber. Atomization occurs at a pressure between 1,500 to 4,000 psi.
2. Lubrication System
Various purposes of lubrication include:
- Reduces the wear and prevents seizure of rubbing surfaces
- Reduces the power needed to overcome frictional resistance
- Removes heat from the piston and other parts
- Separates piston rings and cylinders
- Removes foreign material from the engine
In this system, the engine parts are lubricated under pressure feed. The oil is stored in the oil sump, from where an oil pump takes the oil through a strainer and delivers it through a filter to the main gallery. From the main gallery, the oil flows to the main bearings. After lubricating the main bearings, some of the oil falls back to the sump, some is splashed to the cylinder walls, and the remaining oil goes through a hole to the crankpin. From the crankpin, the oil travels to the piston pin through a hole in the connecting rod web where it lubricates the piston rings. For lubricating camshaft and timing gears, the oil is led through the separate oil line from the oil gallery. The valve tappets are lubricated by connecting the main oil gallery to the tappet guide surfaces through drilled holes. Our FE mechanical exam review course thoroughly explains the fundamental concepts and functional applications of mechanical engineering equipment parts.
Oil Cooler
An oil cooler is used for cooling lubricating oil. Higher temperatures will reduce the viscosity of oil, which causes a harmful oil film to form between moving parts. To eliminate this, an engine oil cooler is used.
3. Intake System
Air flows into the cylinder bore through the following path:
Air cleaner -> Turbo charger -> Intake manifold -> Inlet port -> Inlet valve -> Cylinder bore
- The air cleaner is a filter that prevents dust from entering the cylinder bore. Filters generally have pores on the surface, which are measured by microns. The lowest micron value typically has better filtration. A filter set contains outer and safety filters in heavy diesel engines for better filtration.
- The tuber charger is a very important part in an engine that compresses air from the air filter. Turbo chargers have two impellers fixed on the same shaft. These impellers are driven by exhaust air. Generally, the air sucked in by the air filter is compressed before entering the cylinder bore, which results in high efficiency. The shaft will rotate at the speed of approximately 100,000 rpm to result in a longer engine life.
- The intake manifold is a pipe that transports air from the turbo charger to the inlet port.
- The inlet valve is a valve that allows air into the cylinder bore. The opening and closing of the valve is controlled by a camshaft.
Ready to test your knowledge? Explore our practice exams now!
4. Exhaust System
Exhaust gases flow through the following path in an engine:
Cylinder bore -> Exhaust valve -> Exhaust port -> Exhaust manifold -> Turbocharger -> Muffler
- To reduce engine noise, the exhaust is passed through the muffler. The exhaust gases have a higher pressure than atmosphere; if these gases were to be released directly to the atmosphere, a loud, unpleasant noise would sound, similar to the sound of firing a gun. The muffler is used to cool the exhaust gases.
5. Cooling System
There are many purposes of cooling an engine, including:
- To maintain an optimal temperature for efficient work in all conditions.
- To avoid excess heat and to protect engine components including cylinders, cylinder head, pistons, and valves.
- To maintain the lubricating property of the oil.
There are two types of cooling:
- Air cooling
- Water cooling
Every cylinder in an engine is surrounded by water jackets. The water in the jackets absorb heat from the cylinders. The heated water conducted through the radiator helps cool the water.
There are three types of water cooling methods:
- Direct or non-direct method
- Thermosiphon method
- Forced circulation method
Mechanical engineers preparing for the FE exam are strongly encouraged to review heating and cooling systems prior to taking the FE Mechanical exam.
6. Electrical System
The electrical system of an engine is comprised of the following parts:
- Starter Motor
- Alternator
- Battery
The starter motor is used for rotating the flywheel. A starter motor receives its power supply from the battery. The pinion of the starter motor engages with the teeth of a flywheel ring and rotates, which then rotates the crankshaft. This rotation of crankshaft leads to the movement of pistons in the cylinders. The piston will suck air and fuel into the combustion chamber, which causes the engine to start. After reaching a specific rpm, the starter motor withdraws its pinion from the flywheel.
The alternator is fixed on the engine and includes a pulley. The belt is used to drive the shaft of the alternator. The main job of the alternator is to charge the batteries.
In general, two batteries, each with a 12 volt capacity, are used.